(プレスリリース「Factory of the Futureの実現に向けた製造DXについて 」 別紙)
(プレスリリース「Factory of the Futureの実現に向けた製造DXについて 」 別紙)
取り組みの実例の詳細
すべての患者さんのために(Patient):
IoTを用いた予知保全(大阪工場)
当社の複数の主要製品の製造では複雑な機器である凍結乾燥機を用いており、故障などのトラブルが発生すると基準通りの製品を製造することができなくなるリスクもあります。 大阪工場では2021年度に凍結乾燥機の一部として使用されている真空ポンプなどの回転機器に振動センサーを導入し、状態監視を開始しました。2022年10月にはドライ真空ポンプの振動値が基準内での上限に近づき始めたことが測定データから確認されたため、生産計画に影響を与えない直近のメンテナンスタイミングで軸受けの確認をしたところ、摩耗していることが分かりました。新品の軸受けに交換した結果、振動値が正常域まで低下したことが確認されています。振動センサーを用いた回転機器の集中監視が機器の健康状態をタイムリーに把握し、機器トラブルの予防、ひいては医薬品の安定供給に寄与することが示された好事例となります。
ビッグデータを活用した収量改善(光工場)
当社の光工場における原薬製造には200種類以上の製造パラメータが関与しています。従来はこれらをラボ実験で個別に検証し収量向上を試みていましたが、パラメータ数が多いため、収量に影響を与える要因の特定が困難でした。 本取り組みでは、製造実行システムやラボ情報管理システムなどからの製造データや品質データ、さらには気象データなどの外部データをクラウド環境で統合し、多変量解析や機械学習を利用してより高精度な収量予測モデルを構築しました。このモデルの出力結果と、これまで現場で蓄積してきた知見を融合することで収量に影響を与える重要なパラメータを十数個まで絞り込み、その中でも冷却時間が特に重要であることを特定しました。この分析結果を受けて冷却水バルブの開度を最適化するように現場の作業手順を標準化することにより、収量の4.0 % 増加を達成しています。これにより、同じ原料からより多くの患者さんへ製品をお届けすることが可能になります。デジタルツインによる収量改善(スイス・ヌーシャテル工場)
ヌーシャテル工場では、血漿分画製剤の製造において、不純物を除去する重要な工程で回収率の低下による生産性の課題があり、結果として患者さんにお届けできる医薬品の最大量を達成できていませんでした。そこで、2022年度よりデジタルツインを活用した生産プロセスの分析を開始しました。
本ツールは、企業データバックボーン(EDB)から収集されるデータを用いて、生産ラインのボトルネックや非効率的なプロセスを特定し、改善のための実証済みのソリューションを提供します。特に低回収率の課題に対しては、デジタルツインを使って根本原因を特定し、機械学習モデルを活用してプロセス全体を最適化しました。
その結果、2023年初頭には、不純物除去プロセスでの収率が大幅に改善され、生産性が向上しました。これにより製造の中断が減少し、より多くの患者さんに医薬品をお届けすることが可能になります。
ともに働く仲間のために(People):
AR技術を用いたトレーニングで新製造施設のPPQの成功に寄与(光工場)
光工場では、主要製品の新製造施設の初回生産(Process Performance Qualification: PPQ)をAR技術の活用で成功裏に完了しました。PPQは新設備の製造方法や規格が効果的に機能するかを確認する重要なステップです。光工場に設置された新製造ラインは「シングルユース機器」を用いて高い製品品質を保証していますが、操作手順を必要とするもので、かつ、当時の現場オペレーターにとっては使用経験のないものでした。
AR技術を用いた機器操作トレーニングにより、オペレーターはオフィスでも製造作業を仮想体験でき、より直観的に操作手順を学ぶことが出来るようになりました。この取り組みにより、シングルユース機器を使った初回生産での作業ミスはゼロとなり、高品質な製品の安定供給が実現しました。
実空間の映像の重ね合わせて表示されているトレーニング対象機器(左)と、タブレットデバイス越しに見た様子(右)
VR技術を用いた無菌性環境トレーニング(大阪、光、成田工場を含む全サイト共通)
無菌製剤の製造は高度な無菌性環境下で行われるため、オペレーターは環境を乱さない動作を習得する必要があります。トレーニングは、無菌環境への入室方法、消毒、菌の飛散防止の知識・スキル習得など多岐にわたりますが、実際の医薬品製造に日々利用されている実環境でのトレーニングは困難であり、トレーナーの負担も大きいのが課題です。VR技術を活用することで、オペレーターは仮想空間で無菌環境を体感しながら一人でも実践的に学ぶことができます。この方法により、学習頻度の確保が容易になり、短期間で必要な知識とスキルを習得できるようになりました。
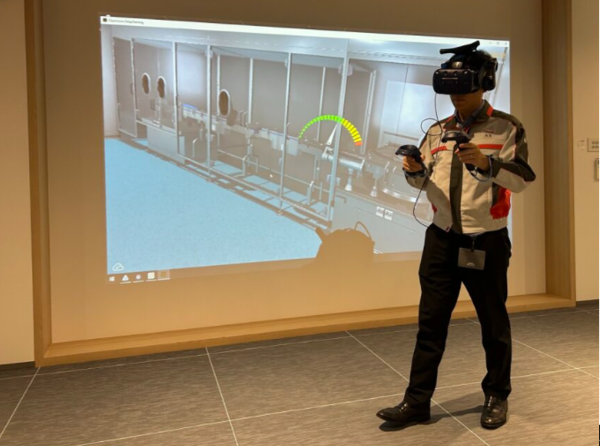