Attachment to the Press Release “Driving Manufacturing DX: Paving the Way to the Factory of the Future”
Attachment to the Press Release “Driving Manufacturing DX: Paving the Way to the Factory of the Future”
Real-world examples
Predictive Maintenance Using IoT (Osaka Site)
In manufacturing some of our key products, we rely on complex equipment such as freeze dryers, where failures can put the entire batch at risk of disposal. In fiscal 2021, we began monitoring the condition of this equipment at our Osaka Site by attaching vibration sensors to rotating components, like the dry vacuum pumps in freeze dryers. In October 2022, our data indicated that the vibration levels of these pumps were nearing the upper threshold. During the next scheduled maintenance, we inspected the bearings and discovered significant wear. After replacing the bearings with new ones, the vibration levels returned to normal. This case illustrates how centralized monitoring with vibration sensors can contribute to the timely detection and prevention of equipment failure, thereby supporting the stable supply of pharmaceuticals.
Yield Improvement Through Big Data Utilization (Hikari Site)
There are over 200 manufacturing parameters involved in the production of active pharmaceutical ingredients at our Hikari Site. Previously, we tried to improve yield by testing individual parameters in lab experiments, but the sheer number made it difficult to identify key factors.In this initiative, we integrated manufacturing data, quality data from our manufacturing execution and laboratory information management systems, as well as external data such as historical weather data in a cloud environment. Using multivariate analysis and machine learning, we built a more precise yield prediction model. By combining the model outputs with field expertise, we narrowed the significant parameters down to a dozen and identified cooling time as a particularly important factor. After standardizing operational procedures to optimize the cooling water valve opening, the site saw a 4.0% improvement in yield, allowing us to deliver more products to patients using the same raw materials.
Yield Improvement Using Digital Twin (Neuchatel Site, Switzerland)
At our Neuchatel Site, we faced productivity challenges in the production of hemophilia treatments due to low recovery rates in a crucial impurity removal process, resulting in fewer medicines for patients. To address this, we began analyzing the production process in 2022 using digital twin technology. This tool utilizes data collected from the enterprise data backbone (EDB) to identify bottlenecks and inefficiencies in production, and provides proven solutions for improvement. Using the digital twin to address low recovery rates, we identified the root cause and optimized the entire process using a machine learning model. By early 2023, this approach significantly improved recovery rates in the impurity removal process, increasing productivity and reducing interruptions during production, enabling us to deliver more medicines to patients.
AR Technology Used for Successful PPQ in New Manufacturing Facility (Hikari Site)
At our Hikari Site, we successfully completed the Process Performance Qualification (PPQ) for a new manufacturing facility using AR technology. PPQ is a crucial step in ensuring that the manufacturing methods and standards of new equipment are effective. The new line at the Hikari Site, which produces high-quality products with single-use equipment, required operational procedures that were new to operators.
Through AR-based training for equipment operation, operators could virtually experience manufacturing tasks and learn procedures more intuitively, even from their offices. As a result, there were zero operational errors during the initial production using single-use equipment, contributing to the stable supply of high-quality products.
The training target equipment (left) overlaid on real-world footage, and the view through a tablet device (right)
Sterile Environment Training Using VR Technology (Applicable to All Sites Including Osaka, Hikari and Narita Sites)
The manufacturing of sterile pharmaceuticals requires operators to master movements that do not disrupt the sterile environment. Training includes topics like entering sterile environments, disinfection, and preventing microbial dispersion, which can be challenging and burdensome for trainers.By using VR technology, operators can learn independently in a virtual sterile environment, allowing them to practice more frequently. This speeds up the process of acquiring the necessary expertise and skills.
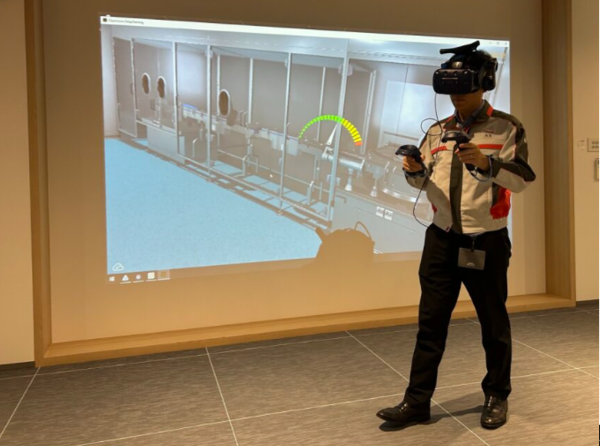